The History of Defense Logistics Agency Aviation
Si
nce 1942 when the installation first activated as the Richmond General Depot under the command of the U. S. Army Quartermaster Corps, a dedicated, diverse, professional workforce has supported America’s warfighters. Though the installation name has changed through the years, one thing has remained the same, the employees’ commitment to put warfighter support first in all they do.
World War II marked the peak of depot operations with more than 8,400 people employed who were supplemented by 1,200 German prisoners of war housed on a 50-acre camp adjacent to the depot. Employees received, stored and supplied quartermaster, medical and engineering items.
The 1950s and 1960s brought the Korean and Vietnam Wars, reorganization and mission expansion to the depot.
With activation of the Military General Supply Agency in 1960 and its absorption by the Defense Supply Agency in 1962, the depot’s mission expanded to managing more than 30,000 general supply items. Escalation of the U.S. role in Southeast Asia drove the workload increase and another name change for the installation to Defense General Supply Center.
By 1967, DGSC was procuring more than $731 million worth of general supplies, accounting for $800 million in annual sales.
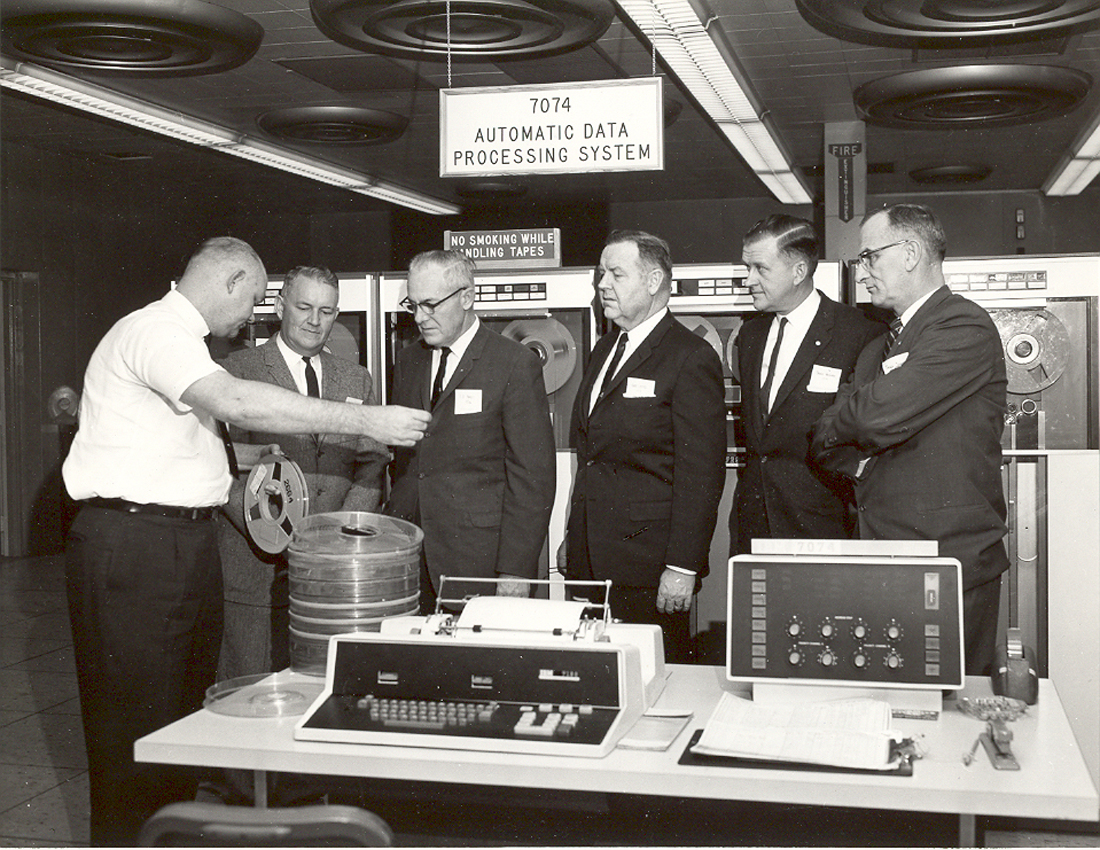
Move Toward Automation
Technological progress was dramatic in the mid-to-late 1960s with four new computer systems being installed that processed more than 4,500 requisitions a day. The center became home to one of the largest data processing facilities on the East Coast.
In the 1970s, workloads increased to include additional federal supply classes such as ecclesiastical and mortuary supplies. In recognition of expanded responsibilities, the installation’s parent organization Defense Supply Agency, changed its name to Defense Logistics Agency in 1977.
In the 1980s, the center’s operations were divided into separate areas for procurement and technical operations. Inventory managers were responsible for an item from start to finish. They received customer demands and forecasts, and generated purchase requests to initiate the procurement action.
By 1984, DGSC developed the Paperless Order Placement System (POPS), the Defense Department’s initial electronic commerce and data interchange application. POPS passed customer requisitions to suppliers for immediate direct shipment from commercial stocks rather than from government warehouse inventories. It also provided same day processing through electronic data interchange increasing sales dramatically in general items like building lighting, batteries and film.
Aviation Focus
In 1985, DGSC assumed management of aviation structural components, laying its foundation as a key contributor to aviation support throughout DoD and through the 1990s, it fielded additional systems to enhance its processes and changed from a functionally-based organization to a commodity-based one.
Professional training empowered employees to make decisions without going to their direct chain of command, and business plans were built to define product center goals. Having groups working the same federal supply classes in the same location allowed for immediate problem-solving. All disciplines came under one umbrella, and employees became multifunctional. Product center leaders learned about each discipline and integrated support team leads had control over the whole product to better support the warfighter.
DGSC also piloted original equipment manufacturer divisions under product centers, allowing for further refinement of business plans and increased communication. Today, OEM divisions are still a critical link in communications with our industry partners.
In 1996, the Defense General Supply Center’s name changed to Defense Supply Center Richmond. Shortly after the new name took effect, agency leaders started talking about supply chain management.
In an initial step toward a supply chain focus, the agency also made federal supply class transfers between field activities. The agency was looking at how it organized work, and the idea of managing by supply chains came into being. The cradle-to-grave approach allowed each supply chain to focus on a certain area, which led to better relationships with suppliers.
Business Systems Modernization
In 2000, Business Systems Modernization (BSM) was formally initiated as a new major acquisition program within DLA that would be a state-of-art system competitive with commercial industry.
In 2004, DSCR employees prepared to manage supply chains, rather than supply classes, through deployment of BSM. Big Bang, the name coined for the deployment and reorganization, affected the entire workforce, physically relocating 2,000 employees on the center and changing job titles for some.
During this time, BSM replaced legacy computer systems to improve customer support, lower operational costs and streamline operations. Completed in 2006, BSM allowed the center to leverage the benefits of commercial off-the-shelf software and reengineered business practices to enhance customer support.
BRAC 2005
DSCR’s mission expanded greatly between 2007 and 2009 with the implementation of Base Realignment and Closure 2005 legislation. The activity privatized its supply, storage and distribution management of tires, packaged petroleum, oil and lubricant products, and compressed and liquified gases. It also broadened its mission as a supply chain provider beyond its traditional wholesale role when it moved into consumer-level retail supply logistics.
During this timeframe, DSCR activated six industrial support activities and five depot-level repairable activities throughout the U.S., moving aviation closer to military industrial maintenance production lines and the artisans performing weapon system repairs.
In July 2010, as part of an enterprise-wide branding campaign, Defense Logistics Agency separated the names of its primary-field level activities from the name of the installations they resided on and the agency’s aviation demand and supply chain previously known as Defense Supply Center Richmond became known as Defense Logistics Agency Aviation, unifying its more than 3,500 employees across 18 U.S. locations and more closely aligning it to the larger DLA enterprise. Defense Supply Center Richmond remains the name of the installation, and is the home of DLA Aviation’s headquarters.
Positioned alongside its military customers, DLA Aviation manages industrial support activities at Robins Air Force Base, Georgia; Tinker AFB, Oklahoma; Hill AFB, Utah; Marine Corps Air Station Cherry Point, North Carolina; Naval Air Station North Island, California and NAS Jacksonville, Florida.
DLA Aviation manages depot-level repairable procurement operations at Robins, Tinker and Hill Air Force Bases; Naval Supply Systems Command (NAVSUP) Weapon Systems Support, Philadelphia; and at Redstone Army Arsenal, Alabama. DLA Aviation also operates an industrial plant equipment maintenance, repair and overhaul facility at Mechanicsburg, Pennsylvania
DLA Aviation also has forward presence employees working alongside its customers in seven other U.S. locations.
The activity’s business functionality consists of six basic core processes representing key functions in supply chain management which enables DLA Aviation to interact, support and meet warfighter requirements. Theses processes are: planning, procurement, order fulfillment, financial management, tech/quality, and customer relationship management.
By focusing on basic business, DLA Aviation is able to minimize supply chain risk, right size inventory and enhance warfighter support. The activity also reduces risks with a deliberate focus on strategic contracting and small business opportunities.
DLA Aviation supports nine major product lines: engines and airframes; instrumentation and gauges, electrical hardware; chemicals and petroleum products; green products; industrial gases and cylinders; ozone depleting substances; topographic, hydrographic, aeronautical maps/charts (digital and print) and industrial plant equipment services.
DLA Aviation delivers unique customer support capabilities through its Industrial Plant Equipment Services (IPES) and Mapping Customer Operations divisions. IPES operates the only industrial plant equipment management facility and maintenance depot in the federal government dedicated to procuring, rebuilding, retrofitting, and repairing metalworking machinery for the Department of Defense and other federal agencies. Mapping Customer Operations delivers exceptional supply and demand chain support by providing digital and print map products to our military services and other geospatial intelligence customers.
DLA Aviation Today
Today, as one of the agency's major subordinate commands, DLA Aviation supports more than 2,341 major weapon systems and is the U.S. military's integrated material manager for more than 1.8 million national stock number items, industrial retail supply and depot-level reparable acquisitions.
In building a rich, proud legacy as a “supplier of choice,” DLA Aviation’s leadership recognizes its success depends on maintaining a strong, diverse, well-rounded workforce focused on warfighter support. DLA Aviation’s culture promotes an environment where each employee, at every level of the organization, has the opportunity to lead every day. Professionalism demands that employees respond to inquiries directly and with the best information available as they continue to focus first on America's warfighter needs.