NSN 1560-00-117-5199
- This stock number was one of DLA's oldest backorders
- Tech data specifies forging is required
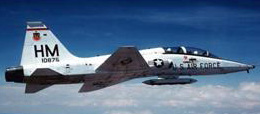
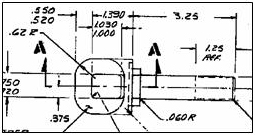
- April 2002, contract award to "Supplier A" who planned to provide a machined part from bar stock. However, the supplier’s First Article did not pass First Article Test.
- Even after the contract delivery date was extended "Supplier A" still could not produce compliant parts so the contract was cancelled July 2004;
- As part of an AFCAT assistance request FDMC located a capable supplier in their National Forging Tooling Database;
- November 2004, DLA Aviation issued contract to "Supplier B" the capable supplier; and,
- 30 days after contract award, "Supplier B" delivers acceptable parts.
Time Savings: 100 to 150 days
The following time line indicates that only 9 days elapsed between finding the tool and placing an order. October 11, 2004 – Request from Becky Bigger at Prop Shaft Supply, Inc for a forge part with NSN 2520-00-796-3997 (part number 7962742) October 12, 2004 – Russell Beard, FORGE-IT Team Leader, checked the NFTD and found the forging company (IMT Forge - a Forging Industry Association Member Company) with the tooling and called the company to verify that the tooling was on-hand. October 20, 2004 - Received verification from IMT Forge that an order for the part had been received. Cost Savings: $15,000 to duplicate the tooling.
Forge Shop Customer
“This database in invaluable to companies like myself, that do work for the US military. This last forging I ordered is a 70 piece order. There is no way, we could afford the time and expense of creating new tooling, especially when there is existing tooling somewhere out there. We do the bulk of our contracts for the military, in small run, short lead-time replacement parts, for older equipment. We manufacture drive-shafts and components. If we cannot find tooling for some of these jobs, we are forced to rough machine bar stock, heat treat, and then comeback and finish machine. Sometimes 2 or 3 rough machining ops are required depending on the type of part. This process leads to increased expense, and lead-times for our military, sometimes the expense is 10 X the cost, due to excess material, and machining operations. Sometimes, the required material is not available, except in billet form, and the part cannot be made from bar stock. This requires a deviation from the Military, and you can imagine how difficult and sometimes impossible that is. Please continue your work on this project. It benefits, not only govt. contractors like myself, but also the military, and the forging houses, that are storing this old tooling instead of running jobs with it, while big run jobs are outsourced overseas. I see this project as a benefit for all involved."